How to Manage Project Risk like a Seasoned Engineer
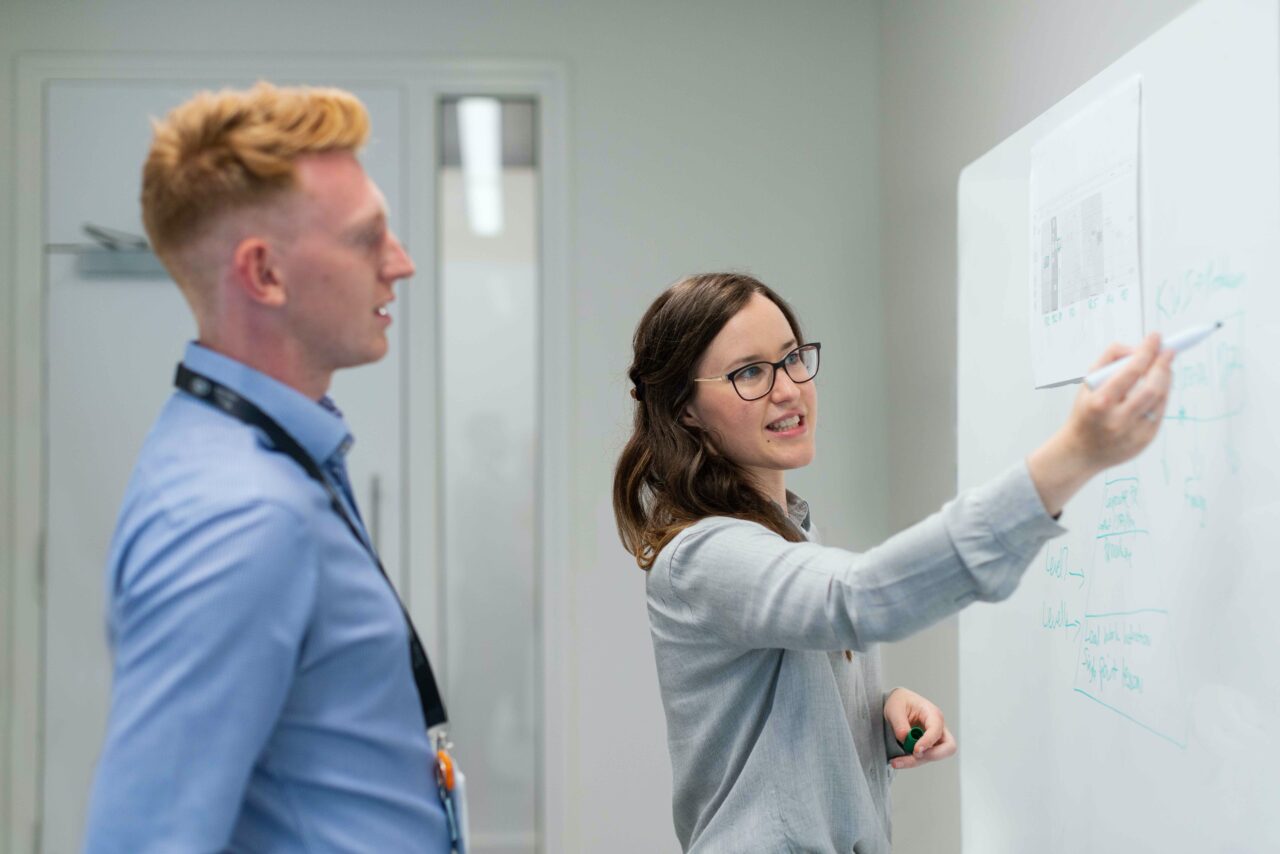
Most engineers approach risk management with a ho-hum attitude.
If you’re an engineer, then this probably isn’t your favorite task. For some, risk assessment is just a formality – a report passed around by different departments. So, you might take this routine easy, letting minor issues go untethered. This causes problems as those minor issues stack and becomes larger. As a result, the organization suffers a loss in both time and money.
Instead, you could avoid this with a well-executed risk assessment.
By addressing high-risk areas through a project’s lifecycle, you can save a company from disaster. This takes the hand of a seasoned engineer.
Are you about to launch a new injection molding project? Want to see how our team performs its risk assessments? Then buckle up! We’ll take you through our 9-Step Risk Assessment Process for assessing a new project request.
1: Part Design
For starters, most injection molded products follow a set of design rules. We call these Design for Manufacturing Principals or DFM. In essence, products that follow these guidelines are easy to produce and offer other molding benefits. This includes reduced scrap rate, less material use, and quicker production cycles.
The first thing we do is evaluate a drawing (or CAD) we receive for manufacturability. This process starts with looking at the product’s geometry. We do this to identify any details that are “difficult to mold”.
For example, wall thickness is one common design flaw we find in drawings. A thick wall can cause product deformation in the form of sink. And deformed products are destined to fail in the field, so we don’t want to encounter that issue!
Similarly, critical dimensions with tight tolerances are tricky. This is because of plastics’ ability to shrink. To clarify, as the product cools it shrinks based on the material’s properties. As a result, the product can shrink past the print’s callout. Of course, this is harder to avoid but doesn’t prevent us from making the product.
Instead, a subtle design change in the early stages will negate this issue before incurring avoidable costs. The result: good product with minimal engineering costs.
If you’re unsure about your part design, you can work directly with us to work out any questions you might have. Alternatively, you can look at conducting a mold flow analysis– a program that simulates how the design will fill in an injection molding environment.
2: Materials
Not everyone is an expert in material science, and you don’t need to be. But having a good understanding of the material you are working with goes a long way towards reducing your risk. You should identify whether the material you want to use is compatible with the application. Otherwise, the consequences of purchasing the “wrong material” can set your project back financially and timewise.
One of the obvious questions you should ask yourself is: “Does this material’s physical and chemical properties meet all my engineering requirements?” In other words, you’re asking yourself whether the material will work under the product’s normal operating environment. You can’t run plastic that has a low melting point in a high heat environment… It’s going to fail. But you already know that!
While that last example might be a no-brainer, some questions don’t come as easy. Here’s our top 3:
- Material Availability – What does the availability of this material look like? Supply chains are as fluid (and unpredictable) as ever these days. Also, some materials require a Minimum Order Quantity (MOQ) which can impact the cost.
- Process Compatibility – This comes into play with secondary processes such as over-molding or ultrasonic welding. Does the material you selected play well with others?
- Dimensional Stability – Does your product require tight tolerances? Well, a well-known quality of plastic is that it shrinks! The amount that plastics shrink varies between each material and each formulation. Just something to keep an eye on!
Ultimately, your best resource for plastic is a materials supplier. Our network of materials suppliers can offer design guides, datasheets, spec sheets, and more. We often involve these suppliers early in the process just so we have all the necessary information in hand and can eliminate potential risks.
3: Tooling
When looking at risk assessment for a new mold build, we exercise a lot of information from other areas that were covered in the previous sections. This includes part geometries, material selection, and labor usage (see automatic molds vs operator-required molds). The goal at this stage is to confirm that the mold’s capability matches the project’s requirements in terms of value, volume, and efficiency.
For instance, one way we facilitate harmony between reality and expectations is through production volume. If your annual production volume is less than 25k parts, then you’ll likely want a prototype quality tool. In contrast, if you’re looking at +1 million parts, you’ll want to upgrade into production tooling to avoid doubling down on your mold investment.
Another great point is building the mold with the right materials and features. When we talk about steel materials, we look at the chosen material’s physical and chemical properties. You don’t want a glass-filled material running thousands of shots in an aluminum mold because it will wear faster. With mold features, you can underestimate the labor cost of a mold with multiple hand loads and other manual-intensive features.
Plastics Plus manufactures all its tools to SPI specifications. And because any tooling built and retained is maintained at no cost to the customer, it is in both of our interests to conduct a full risk analysis and mitigate any risks before turning on the build.
4: Labor
Labor might not strike you as a risk factor. But the truth is – labor can be sneaky and costly when unaccounted for. There are a few circumstances where we try and address any labor risks, so let’s dive a bit deeper.
Part and Tool Design: good manufacturing design principles will tell you that fewer components in any given assembly are ideal for manufacturing. How does this relate to labor? Well first, more components will require more labor-intensive activity like degating, deburring, trimming, machining, welding, and more. This introduces the possibility of variation and mistakes in handling the product.
Then, we must consider the risk with the actual assembly of the product. The further along down the production lifecycle, the more valuable the product is and the more expensive it is to lose on defective parts. Ultimately, we look at the risk associated with performing the entire assembly along with the possibility of not having enough people to do them. This is especially an issue with the current labor shortage.
For tool design, we look at whether the tool is automatic or not. The question we ask is “does an operator need to stand in front of the machine to do XYZ”. If not, then the machine can run without operator supervision (aka does not use labor resources). If the mold has multiple features, like hand-loaded inserts, then that requires much more labor.
Physical Injury: Good Manufacturing Practices (GMPs) and OSHA standards cover most common workplace accidents, and we value injury prevention as much as any manufacturer. But as we mentioned above there are inherent injury risks present with labor. And the injury doesn’t always happen at work. An injury can occur on the factory floor, or it can occur outside of work during a pickup game at the YMCA. Either way, injuries are a risk we must consider as it contributes to a strained workforce.
*Just a note: we rotate positions on our production floor for this reason. It’s unlikely someone will sustain a serious injury, but it’s a risk that is still present.
5: Equipment
Equipment failure isn’t something we run into often. However, the inherent risk with unplanned downtime due to equipment failure must be considered in the risk assessment. Unplanned downtime due to machine failure or mold damage happens for a few reasons: One – the equipment runs past its expected lifetime and requires repair or replacement. Two – the machine does not function as intended because of numerous factors. To prevent the latter, we test and validate our processing procedures to reduce human-caused errors. Furthermore, we keep a detailed maintenance database to check the pulse on all our equipment.
Another risk we consider is sourcing a new piece of equipment. For example, a new project might require a minor investment in equipment such as a fixture. Another might require us to buy an entirely new piece of production equipment like a heater or dryer. In either circumstance, we are at the mercy of our supplier. If the lead time on that equipment is extensive that poses a huge risk to the project’s timeline. Under those circumstances, the cost due to lost time can result in thousands of dollars. Therefore, we do our due diligence to ensure that we receive and can operate the required equipment for your project.
6: Packaging
By working with Plastics Plus, you have the option to produce a finished, packaged product. In other words, your product can be molded, assembled, and packaged all under our roof and shipped to you ready for market. This is a great advantage for you as the product owner, but it doesn’t come without risk.
The risk in packaging is a combination of a few other risk areas that we’ve covered in this article. For example, let us examine the packaging equipment. A complex packaging machine can do a few things at once: unroll, print, open (with air), and seal the package within a single cycle. Any variation in this process will impact the quality of the packaging and potentially the product. And any machine failure will result in unplanned downtime. In either case, the result is a loss of time and money.
Now let’s look at this from a materials standpoint. As with most supply chain constraints, not being able to source the packaging is the primary risk. The secondary risk is sourcing poor-quality packaging that doesn’t meet either of our standards. If we added a third risk, it would be scrapped packaging. All three of these situations pose a risk to our operations. But more importantly, it poses a risk to your bottom line which is what we are aiming to improve in the first place. Before we jump into one more area of packaging risk, we should remind you that our quality system is designed to prevent the poor product from ever reaching your doorstep. Thus, you can be confident will address any major concerns upfront.
No one likes to be blindsided by poor foresight.
Since we mentioned shipping to your doorstep, we should address the risk with shipping products. When we ship products via courier there are a few things that can happen. For instance, products on long-hauls can be damaged on their route because of poor handling. Nevertheless, we contract with major courier services to ensure that a professional is handling the product. Ultimately, the risk here is minimal but needs to be considered as part of our process.
7: Application
Application, or the end-use of the product, is one of the most important portions of our risk assessment process. We need to collect as much information on the use of the product and the environment as possible. During our initial conversations, we will expect to learn exactly who the end-user is and what the impact of the product is. Furthermore, we will want to identify the level of safety (or danger) for the user. On a similar note, we will consider whether the product is fit to function in its intended application.
For example, products that come into direct contact with a medical patient (such as a cannula) carry a higher risk factor than a plastic clip. Similarly, if the component is critical to the operation of an assembly or device (such as a CPAP) then the risk is also high.
Comparatively, if the product does not interface with the user and has low criticality then the risk factor is lower. Nevertheless, we still evaluate whether the product can be successful in its normal operating environment. Just because the risk for injury or death is low, we still want to prevent product failures. In this case, we’ll look at the fit and function of the part from an engineering and materials standpoint to identify any red flags. Ultimately, it is your job to determine whether the product is fit for purpose.
For review, we covered three application risks in this section:
- Risk to the user
- Risk of criticality
- Risk of fit for purpose
Next, we’ll cover risks associated with compliance and quality requirements.
8: Regulatory Compliance
Regulatory compliance isn’t necessarily a risky undertaking for most projects. FDA compliance, GMPs, and other regulatory/ statutory requirements are handled primarily on your end. But we often abide by the same requirements to give our customers a seamless experience. However, these requirements prove to be more stringent for some products than others. Some of these falls outside of our capabilities, namely controlled molding environments and ISO-certified clean rooms. Under those circumstances, we avoid risk by turning the project away. On the other hand, we assess projects within our capabilities and determine the risk of falling out of compliance. All things considered, our quality department ensures that our party abides by all requirements laid out by you, the customer.
9: Special Quality Requirements
Validation is a staple in any robust Quality Management System (QMS). This is a multi-step, cross-departmental function in most manufacturing companies. It proves the capability of the methods machinery used to produce, measure, and test the manufacturing outcomes. In other words, the quality requirements set forth by the customer are fulfilled through validation procedures.
When we consider the risk inherent in those quality requirements, we look at the capabilities of our staff, equipment, and processes. These risks are like those present with regulatory compliance in that every product is a bit different. The first thing to consider is whether we can meet the proposed quality requirements. Some products carry tight tolerances in their drawings, critical dimensions that are unavoidable. Although we specialize in close-tolerance injection molding, we encounter some dimensions that are outside our capabilities. Once we establish competency to meet those requirements then we show our proof in the pudding. Explicitly, we’ll run our tests (IQ, OQ, PQ) and conduct others as required (PPAP, MSA, DOE, etc.).
If you want more information about our quality procedures, you can follow the link here.
Conclusion
By now, you should have a grasp of all the elements of proper risk assessment. Congratulations! You’re on your way towards approaching risk like a seasoned pro.
Good luck with your next project! Contact us if you need help conducting a full risk assessment on your next injection molding project.
Want more engineering tips? Follow our newsletter by clicking the link here and get tips from our engineers delivered straight to your inbox.