8 Ways to Control Your Validation Overhead Costs
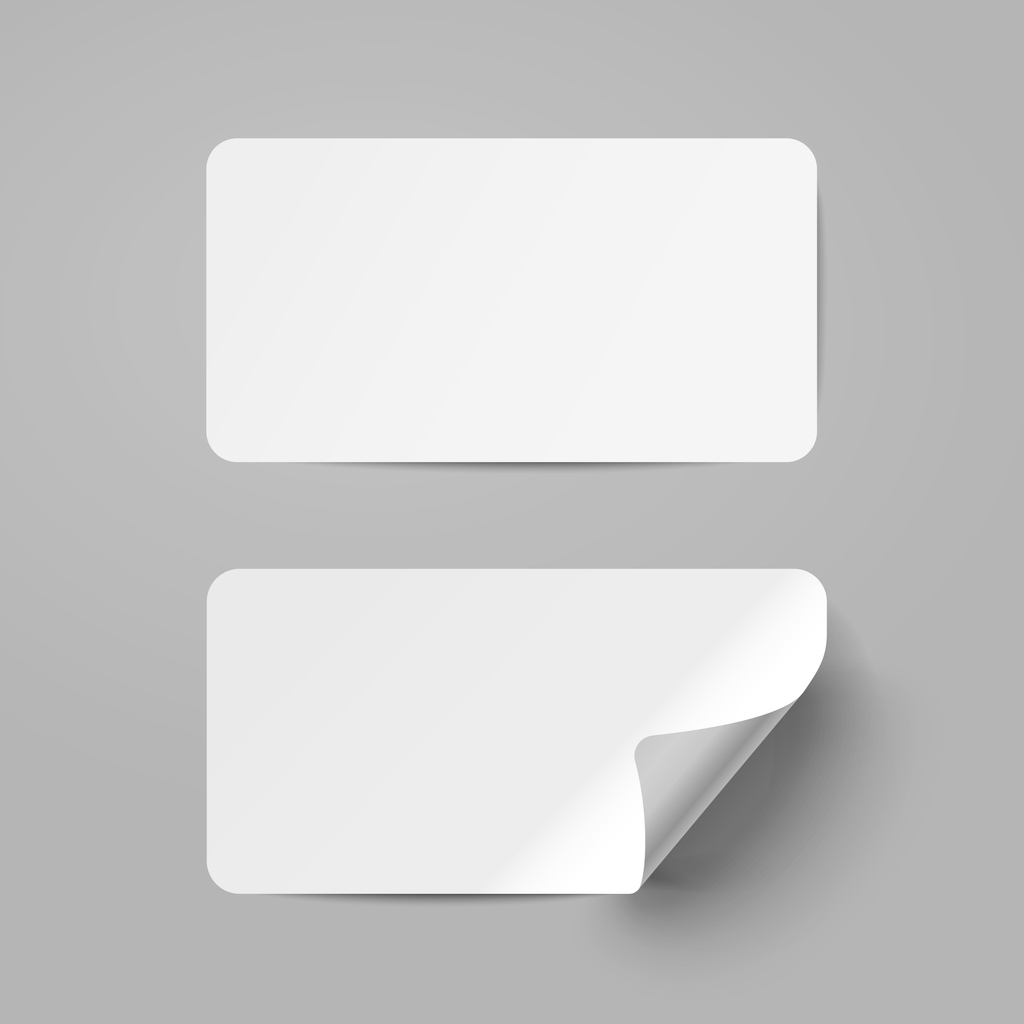
Summary
8 ways you can keep your validation overhead costs controlled.
The validation process is like a charcuterie board of overhead costs… And if your quality requirements are stringent – you’re going to need an appetite.
When looking at the overall cost of an injection molding project, it’s easy to quantify and even justify the costs of upfront tooling. Same with the price per unit of each part. But when we start talking about validation processes, things are not always as clear. Therefore, costs can easily begin to compound when the process is not monitored and carried out properly.
First, you want to have the right people.
Validating new products and components requires oversight from Quality and Engineering SMEs. These experts are no slouches – often leveraging specialized skills in processing, measuring, data analysis, and other high-value skills. Their time and knowledge are worth their weight as long as the processes and systems they have to follow can make the best use of them.
That’s where having the system to test, record, assess, and the document becomes so valuable.
It will help you plan, check, and monitor your expenses throughout the validation process. This allows you to make quicker, more informed decisions to stay on budget.
If not, then validation overhead could end up being a significant (or even the biggest) cost driver. You don’t want this process to eat up all your budget.
💡 Here are 8 ways you can keep your validation overhead controlled:
🔎 Utilizing industry standards and guidelines for validation, such as ISO 13485 and ISO 9001, to ensure that all necessary validation processes are being followed.
🚨 Implementing a risk management process to prioritize and focus validation efforts on the most critical aspects of the device.
🚌 Streamlining validation protocols and procedures to minimize duplication of effort and increase efficiency.
💻 Automating validation testing and record-keeping, using electronic systems to reduce manual errors and increase accuracy.
🔎 Continuously evaluating and improving validation processes to ensure that they are current and effective.
🤩 Outsourcing validation services to third-party providers, which can provide specialized expertise and resources.
🔧 Using a modular approach in design, where different parts of the device are validated separately, which can reduce the overall validation effort.
📄 Utilizing device history records, which can provide a detailed record of the device’s history, which can be used to demonstrate compliance with regulatory requirements.
If you struggle to accurately control your validation processes and you’d like to chat about how to improve your process – reach out to us! Plastics Plus Technology operates a QMS that strictly follows ISO 9001:2015 and ISO 13485:2016 requirements.